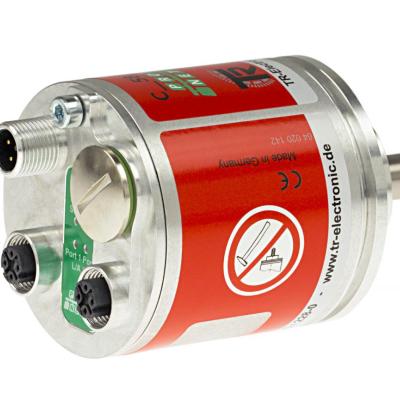
C__582: Standard build with outstanding opportunities.
The new generation of rotary encoders in 58 mm build by TR Electronic offers efficient design combined with state-of-the-art equipment.
As a robust magnetic rotary encoder, it scans a resolution of 13 bit within one turn (single turn) and 12 bit turns (multi turn), optionally 16 bit. The precise optical scan even permits 15 bit or 18 bit in single-turn parts. The absolute value encoders are delivered with servo flange, clamping flange and push-on hollow shaft up to 15 mm; a continuous hollow shaft up to 15 mm is also available with optical scanning.
Installation space is valuable. It is important that the connection lines are not in the way. For the versions with full shaft and push-on hollow shaft (blind shaft), you can choose between the axial cable output (=i.e. on the housing lid opposite the shaft) or a radial one (= on the side of the tube). A cycle time of less than 1 ms for updating of the rotary encoder actual value makes it possible to use the new C__582 without limitation for faster position control. The output is scalable: Broken gear parameters (enumerator/denominator) map nearly any gear factor, even for precise recording of closed round axes. The absolute rotary encoders by TR meet the standards of the respective user organizations for parameterization; Users will find it easy to handle the standard parameters this way. Additionally, free configuration offers simple access to all functions that are available in addition to the standard. The time basis of the speed evaluation can be adjusted freely in the range from one millisecond to one second and can be scaled in any units as well. Knowing about the condition of the system at all times is one of the most important aspects of industry 4.0. No matter if it is about utilization or pending maintenance: C__582 will supply all necessary alarm and diagnosis messages for long-term machine and plant control. The new generation of C__582 industrial standard rotary encoders is consistently equipped with state-of-the-art chip families and supports the latest communication standards for industry 4.0. Preset values are transmitted "on the fly" via the real-time-capable process mapping area. Thus, absolute adjustments (also called "preset" or "offset adjustment") can be performed synchronous with the control cycle even in active plant operation. Axle standstills are no longer required for this.
The new generation of absolute rotary encoders consistently supports modern Industrial-Ethernet versions - currently, these are ProfiNet, EtherCAT and EtherNet/IP - for which further options are integrated.
SUMMARY
The firmware for devices with EtherNet/IP can be updated via the asynchronous TCP/IP. Already-installed devices can be equipped with new functions this way and are therefore ready future-proof for new applications as well. Device Level Ring DLR makes it possible to quickly convert network branches into a highly available ring. A single line from the last subscriber of a branch back to the switch produces a reliable ring in which any interruptions will be recognized and bypassed at once. One cable break per ring will therefore not cause any failure of subscribers behind the cable break.
Free mapping of process data permits application-oriented design of the transfer protocol for users of EtherCAT. With distributed clocks that support a cycle time of >= 100 μs, all sensors and actors involved in a position and track control are perfectly synchronized. Cam signals can be calculated directly in the encoder and integrated into the telegram.
ProfiNet IO-encoders support the encoder profile of the PI standardization organization. They meet the highest real-time standard IRT. Thanks to neighborhood IDs, rotary encoders can be replaced without having to be set up from an engineering tool beforehand. In fast startup mode, a valid position value will be available at the bus only 1.5 s after voltage activation. The media-redundancy protocol is supported for higher availability. Again, a highly available ring is formed by an additional connection from the end of one branch back to the switch. ProfiNet encoders of the C__582-series can either be configured for "Fast-Startup" or "Media- Redundancy-Protocol".
DETAILED INTERFACE
Ethernet/IP
The firmware for devices with EtherNet/IP can be updated via the asynchronous TCP/IP. Already-installed devices can be equipped with new functions this way and are therefore ready future-proof for new applications as well. Device Level Ring DLR makes it possible to quickly convert network branches into a highly available ring. A single line from the last subscriber of a branch back to the switch produces a reliable ring in which any interruptions will be recognized and bypassed at once. One cable break per ring will therefore not cause any failure of subscribers behind the cable break.
EtherCAT
The EtherCAT telegram of the rotary encoder can be adjusted freely in order to meet the programmer's demands. Choose from the actual position, speed, warnings, alarms, software cams, etc. what you need for your process/control architecture. For precise position and track control of moved axles, all sensors and actors involved must be synchronized. This is achieved by distributed clocks in EtherCAT. The smallest possible cycle time in the C__582 is 100 μs. Cams have been used for automation since the industrial revolution. Initially, this was done mechanically by cam discs and vertical shafts, later by electromechanical cam switchgears. Today, cam signals are computed in the control - or comfortably directly in the C__582 ETC. The cam signals are then displayed in the process data image as desired and available to other bus nodes.
PROFINET
C__582 EPN consistently supports the EPN encoder profile. The ProfiNet version relies on the latest technology with long-term availability and is perfectly compliant with the latest standards of the PI user organization. Time-precise synchronization (IRT) permits precisely synchronized positioning of multiple axes. Thanks to neighborhood recognition, you can exchange devices without needing any engineering tools. A newly added rotary encoder uses its neighbors to determine the position that it holds. It can then call the setting data for the rotary encoder to be replaced from the control. The new CM_582 ProfiNet starts within 1.5 s, which is faster than any other bus rotary encoder. Once the project has been set up, a stable, valid absolute position encoder will be available in the ProfiNet control within moments after reactivation of the power supply. System start is massively accelerated this way, and in particular modular machine concepts (with temporarily disconnected modules) profit directly from this technology.
The ProfiNet interface of the CM_582 supports the innovative Media Redundancy Protocol MRP. Usually, ProfiNet only supports a line/tree structure. A redundant connection is not primarily intended for in the standard. MRP considerably increases availability with a single trick! An additional line from the last subscriber to the next switch connects branches into one ring each. The accordingly configured subscribers recognize this. One of the subscribers opens this ring by "ignoring" the second connection. If a connection fails (by cable break or failure of a subscriber), participants will recognize this and try to find another path to the rest of the system. The previously opened connection is now closed and all subscribers are connected to the network again. C__582 EPN can be configured either for Fast Startup or Media Redundancy Protocol.
Absolute rotary encoder C__582 with axial connection field
Absolute rotary encoder C__582 with radial connection field and blind shaft